|
 |
ある一流企業から難題「精度を維持し量産化。ただしコスト軽減は絶対条件」…様々な苦難の中で、FUJITAITOが導き出した具体策とは…! |
|
|
●お客様 |
A社(一流電機メーカー) |
●導入
●システム |
冶具に関する精度・コストパーフォーマンス等の案件に対する対応 |
|
|
|
 |
 |
 |
 |
 |
 |
 |
 |
 |
 |
|
【持ち込まれた案件】
精密IT部品を精度を維持し、大量生産できるベース冶具ができるのか?また、量産品パーツのためのコスト軽減を考えよ。あわせて、製品サイクルが速いため、立ち上げが速く、納入対応が出来るのか? |
|
|
 |
 |
 |
 |
 |
 |
 |
 |
|
|
|
まず考えたことは、 |
 |
|
製品を作る上でクリアーすべき冶具精度は? |
 |
|
製品形状は冶具に安全固定できるのか? |
 |
|
製品生産時に求められる冶具の対応特性条件は? |
 |
|
納入期日の対応条件は? |
|
等の案件に対し、社内で行程検討会を行い、難関をクリアすることで「会社の明日がある」との精進で取り組むことになりました。 |
|
|
|
 |
 |
 |
 |
 |
 |
 |
 |
 |
 |
|
【各々の課題分析】
冶具の形状構造の打ち合わせにおいて、自動化ラインに組み入れられる冶具で、製品が日産数万個対応が出来るようにしなければならない…
? |
|
|
 |
 |
 |
 |
 |
 |
 |
 |
|
|
社内にて製作構想を立案し |
 |
|
冶具個々単位での製作では、加工時間などオーバーペースが考えられるため、冶具を連結タイプで製作する。 |
 |
|
生産性をあげるため、ベースプレートを作り、多数の連結冶具を並べることにする。 |
 |
|
生産工程での加工時に温度変化が著しく(-10〜+80℃)、速やかに対応できうる金属。 |
 |
|
冶具発注から納期が短く、なおかつ数種のパターンが必要である。 |
 |
|
機械加工を行うには、脱着回数を少なくすることが時間とコストの軽減につながると考えた。 |
 |
|
ベースプレートに多数の冶具がついたものを装置に組み込む時、手作業でセットを行うときもあることを想定し、大きさ、重さを考慮する。 |
 |
|
加温などを網領して、金属特性とEを考慮し、アルミ素材で製作を行う。 |
 |
|
試作、量産で安定稼動が実証された後、製品をダイカスト製に移行し、生産性とコストを追求する。 |
|
|
|
|
 |
 |
 |
 |
 |
 |
 |
 |
 |
 |
|
【具体的取り組み】
24時間体制で試作品をテストし、より確実な稼動システムを構築する! |
|
|
 |
 |
 |
 |
 |
 |
 |
 |
|
|
以上の考察案件を提案し、お客様から了承を得て、製作を開始。試作冶具製作、同時に製作冶具の設計、加工を実施。作業効率を高めるため、24時間体制ローテーションを構築。試作品製作→組み付け→稼動テストの繰り返しでノウハウを蓄積し、より堅実な稼動を生み出したのは、図面完成から10日後のことでした。 |
|
|
|
 |
 |
 |
 |
 |
 |
 |
 |
 |
 |
|
【お客様の評価】
稼動時の評価が高く量産化決定。CADシステムの活用で納期も短縮! |
|
|
 |
 |
 |
 |
 |
 |
 |
 |
|
|
約240時間フル稼働で完成させた量産試作品をお客様にご覧いただき、稼動時の評価で大変喜んでいただくことができました。また、二次的要素の金属処理などを取り入れることで、より品質の向上ができるといった個別案件を提示し、即了承を得ることができたのです(これは、スタッフにとっても大変な励みとなったようでした)。 |
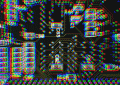 |
また、加工冶具、製品加工においては、CADシステムをフルに活用し、加工工程担当者とダイレクトに情報交換ができたことで、完成時期がより短縮。しかも、量産ダイカストに移行時も、図面対応を迅速に行うことができたのです。 |
|
その後も安定稼動を続け、お客様からはコスト・精度・短納期など各方面の評価を頂き、トータルで20万個のオーダーを頂くこととなりました。初期投資はある程度冒険と覚悟が必要ではありましたが、今回はより以上のメリットが出せたのではないかと考えております。 |
|
|
|
|
 |
 |
 |
 |
 |
 |
 |
 |
 |
 |
|
【本事例のポイント】
従来の約35%以上の納期短縮が可能! |
|
|
 |
 |
 |
 |
 |
 |
 |
 |
|
|
以上は、最近の稼動実例ですが、弊社の試算では提案・取り組みから製品の立ち上げまでトータルして、約35%以上の納期短縮メリットが可能であると確信しています。提案から始まることにより製品及びシステム全体の品質が保証される…FUJITAITOは、お客様に対しより以上の信頼と安心をお約束できるよう、日々改善に努めてまいります。 |
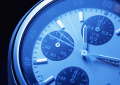 |
|
|
 |
|
|